Research aim 1-4 – heat transfer performance data
Heat transfer test rig design and data (critical step 1-4-1/2-2-1)
A test rig design for heat exchanger performance investigation has been completed and now undergoing review with our industry partner. The rig will use a temporary heat resource and has been configured to allow testing in two flow lines: One for control testing and the other for new design ideas tested against the control. This test rig also incorporates testing capabilities for other Organic Rankine process cycle units, such as turbines and pumps.
Data implementation into EDT (critical step 1-4-2)
A comprehensive spreadsheet algorithm for tube fin heat exchanger design has been programmed in Microsoft Excel. The algorithm has been verified against well-known heat exchanger design software HTRI and is undergoing implementation into the Expert Design Tool format. A trial version will be available for testing by the end of October this year.
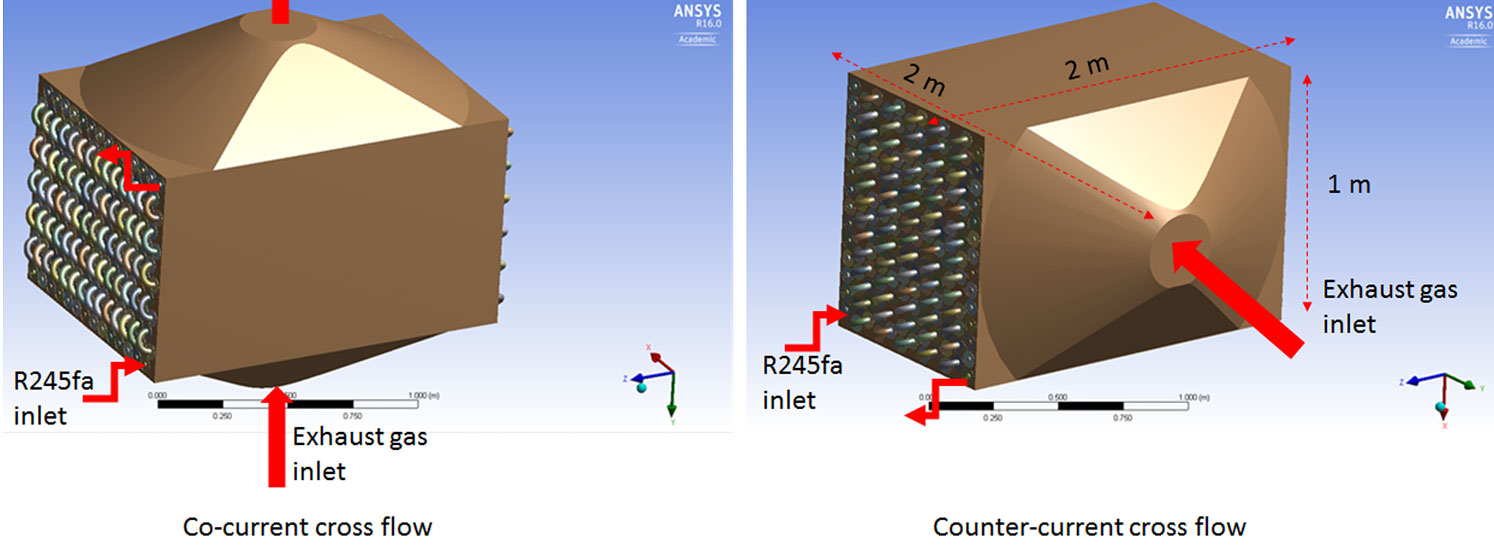
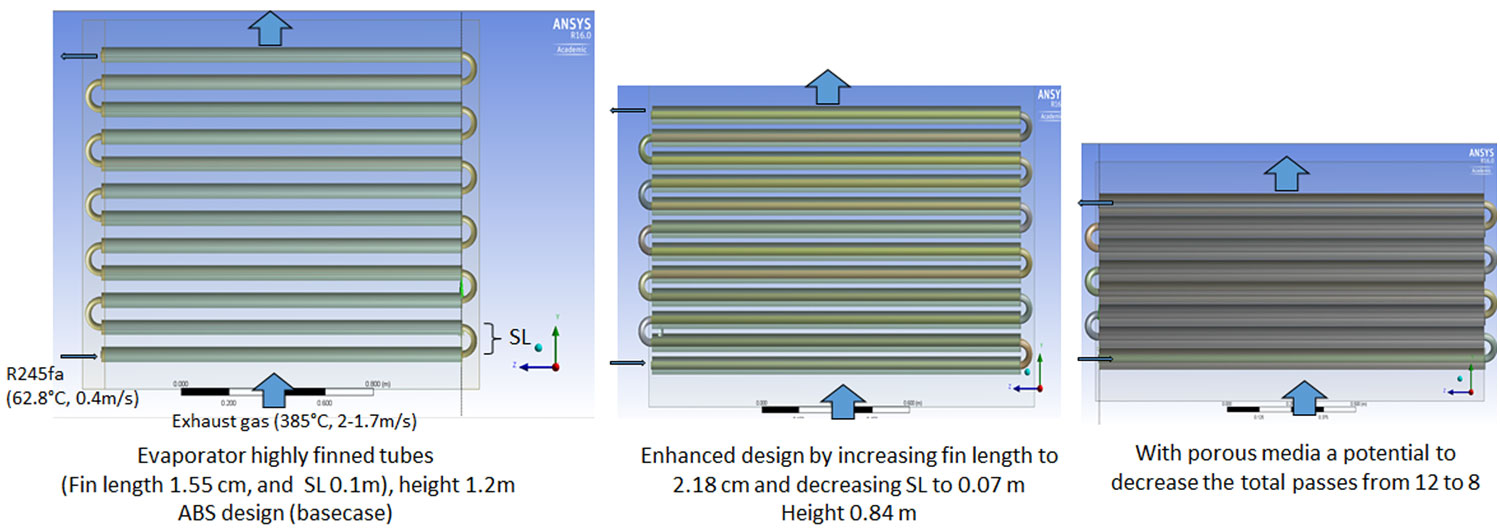
Research Aim 2-2 – AGGAT Heat Exchanger Technology Development
Novel heat exchanger concept 1 (critical step 2-2-2)
The first innovation concept is replacement of an existing sound muffler device around the exhaust gas pipe on a gas engine by a dual purpose sound-attenuating and built-in heat exchanger (evaporator) set-up. A fin-tube heat exchanger was proposed for this application. Fin optimization studies were conducted focusing on fin efficiency and heat transfer co-efficients. The heat exchanger type (co-current / counter-current) was assessed for performance as shown in Figure 1 below. Considerable improvement was confirmed with counter-current design.
A potential of 16% increase in heat transfer can take place by decreasing the gaps and forcing the flow of the hot gas to regions between the fins where the maximal heat transfer is taking place. Similar results can be achieved by increasing the size of the fins.
Novel heat exchanger concept 2 (critical step 2-2-3)
A novel surface enhancement technique is porous media rolls instead of fins. Another technique is to use rough surfaces and corrugated tubes. Of most interest is the porous media option. CFD-assisted research is in progress to ascertain the most suitable option for the application of these novel concepts. The expected enhancement of porous media will have a direct impact on the resulting size of the evaporator, as shown in Figure 2 below.
Novel heat exchanger concept 3 (critical step 2-2-4)
Use of silver-nano particles in refrigerant as opposed to pure fluid in an ORC system can increase power generation by up to 10% across a wide temperature range. The improvement is attributed to the increase in the thermal conductivity of the working fluid.